Architectural Stonemasonry
Skill Explained
An architectural stonemason generally works in the commercial sector, cutting to shape all natural stones (granite, limestone, sandstone and marble) by hand or with Computer Numerically Controlled (CNC) machines.
There is a direct relationship between the nature and quality of the product required and the payment made by the customer. Therefore the stonemason has a continuing responsibility to work professionally in order to meet the requirements of the customer and thus maintain and grow the business.
The architectural stonemason works on heritage sites and in workshops. The work will range from basic places of worship to massive Gothic cathedrals, from simple but significant buildings to the grand architectural and secular commercial and municipal buildings that define a country’s heritage.
He or she will produce stonemasonry components, and undertake letter cutting and carving.
Work organization and self-management, communication and interpersonal skills, problem solving, innovation and creativity, working safely and accurately are the universal attributes of the outstanding architectural stonemason. Whether the architectural stonemason is working alone or in a team the individual takes on a high level of personal responsibility and autonomy.
Mistakes are irreversible and very costly. Every part in the process, from working safely through to exceptional precision, accuracy and attention to detail, is important.
Restoring, conserving, renovating and maintaining cultural and architectural heritage is highly valued for structures that are locally, regionally, nationally and internationally significant. For the talented architectural stonemason there are many commercial and international opportunities; however, these carry with them the need to understand and work with diverse cultures and trends. The diversity of skills associated with architectural stonemasonry is therefore like to expand.
What the Competitors do at the Competition
The Competitor is judged on:
- Templates
- General impression
- Corners, arrises, internal mitres
- Measurements & external mitres
- Flat surfaces
- Profiles, profile surfaces, curved surfaces
- Letter cutting and carving
- Safe working practices
- Interpretation of specifications
The main components of the project include:
- Developing templates to set directly onto the stone in order to measure and mark out equipment.
- Working straight and circular mouldings, external mitres/angles, internal mitres/angles, ashlar stops, weatherings/wash, flat surfaces.
- Transferring the carving and letter cutting detail onto the required surface(s) according to the test project drawings and specification.
Competitors
Brayan BERGER
France
Michael Egli
Switzerland
Marius Golser
Austria
Tae Hun Kim
Korea
Ilmari Manner
Finland
Aogu Mizumura
Japan
Evgeniy Nikiforov
Russia
Djalma Rodrigues
Brazil
Sam Turner
United Kingdom
Jordy Weevers
Netherlands
Gabriel Wellenzohn
South Tyrol, Italy
Experts
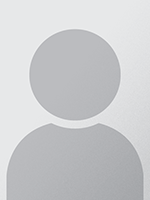
Vladimir Ananev
Russia
Jean-Luc Braun
Switzerland
Kevin Calpin
United Kingdom
Ernst Jan de Vries
Netherlands
Pierre-François GAURIER
France
Bernhard Hasenöhrl
Austria
Jai Soon Lee
Korea
Tobias Nussbaumer
South Tyrol, Italy
Ari Peltola
Finland
Diego Pereira
Brazil
Yasuhiro Shirai
Japan
Videos
A New Look at Skills
Autodesk Publisher 3D models*
Download for desktop
Download for mobile
Autodesk Inventor Data Sets**
* Open the 3D models on desktop with Autodesk Inventor Publisher. On mobile download the Autodesk Inventor Publisher Mobile Viewer app (iOS or Android).
** Students and Teachers can download Autodesk Inventor software via the Autodesk Student Community, Educational Institutions via Autodesk Academic Resource Centre (ARC).